
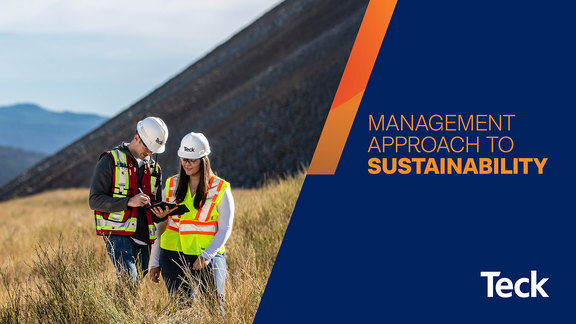
MANAGEMENT APPROACH TO SUSTAINABILITY
Download our Management Approach to Sustainability for information on our approach to material topics
Other Sustainability Resources
Financial and Governance Reports
Ongoing Topics
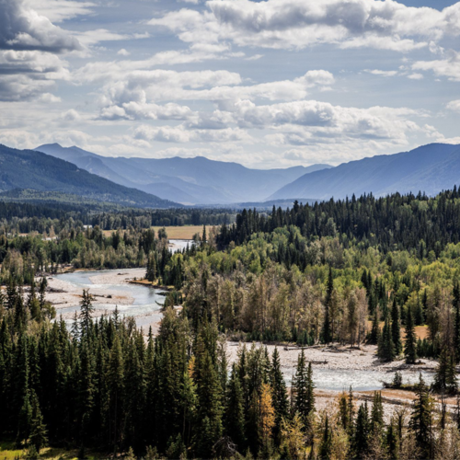
Environmental Management at Trail Operations
Trail Operation’s effluent management, Lower Columbia Ecosystem Management Program, Aquatic Receiving Environment Monitoring Program, Upper Columbia River Project, Groundwater Remediation Plan, and more.
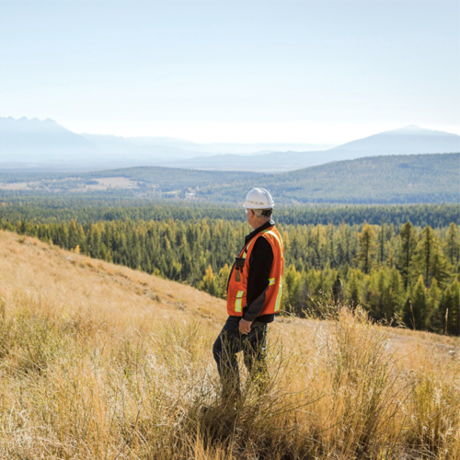
Reclamation and Legacy Site Management
We begin planning for responsible mine closure before mining starts, and that work carries on throughout the lifecycle of the operation, in cooperation with Indigenous Peoples and local communities.